How one of Latin America's largest truck and bus manufacturers is using Linear Programming to make its assembly line more efficient
- Denis Pesa
- Feb 26
- 5 min read
Automation data collection Optimization of the decision-making process Results with clear and accessible presentation
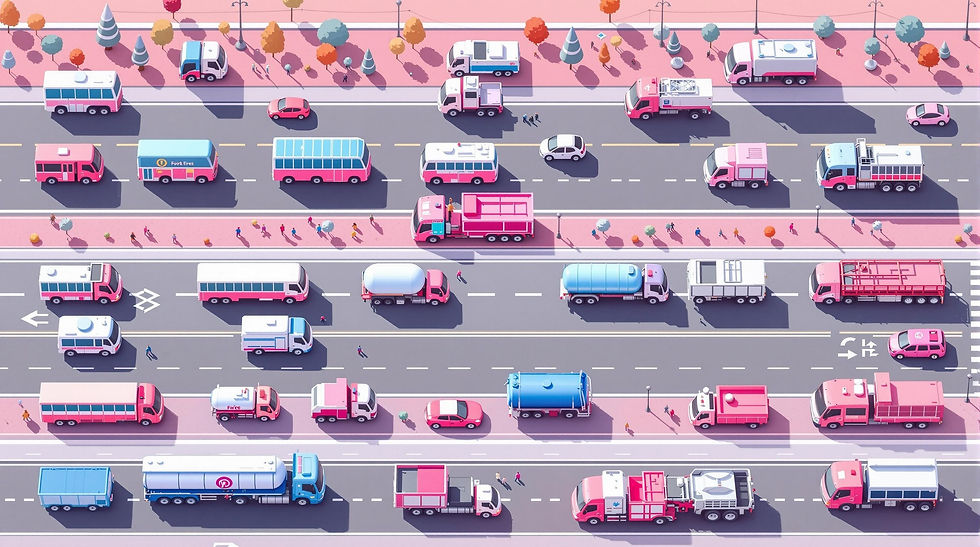
AI generated summary:
One of Brazil’s largest manufacturers of heavy commercial vehicles was looking to optimize its production planning to increase operational efficiency and reduce costs. Facing challenges such as lengthy manual analyses and impacts on productivity, the company adopted a solution developed by BlueMetrics. Using optimization algorithms based on linear programming, the platform automated critical processes, reducing analysis time from 4 hours to 6 seconds and improving operational predictability.
Overview
Our client has been in business for nearly half a century and is one of the largest manufacturers of heavy commercial vehicles in Brazil, with a strong presence throughout Latin America. It produces a complete line of buses and trucks, with a gross vehicle weight ranging from 3.5 to 125 tons, divided into three families. The manufacturer has also developed a complete line for passenger transportation, focusing on the rural, urban, charter, highway and school bus markets.
In a sector where operational efficiency is essential to maintain competitiveness, the company identified an opportunity to optimize its production planning process to meet market demands with agility and precision.
According to Gabriel Casara, CGO of BlueMetrics, “We were called in to help solve a problem that is crucial for any company in the industrial segment: the need for greater process efficiency, which translates into operational gains and profitability. And for this, the solutions we have developed in the areas of AI, Machine Learning and Process Optimization proved to be ideal.”
To address the challenges of managing thousands of components and vehicle model combinations, as well as reducing the time spent on manual feasibility analysis, BlueMetrics implemented the Tech Storm solution for this manufacturer. Developed to automate and optimize critical processes, the platform allowed the factory to increase productivity, reduce costs and improve operational predictability.
Problem: How to make operational processes more efficient and automated?
As with any industrial assembly line that deals with complex processes and automation, production planning for this industrial customer faced significant challenges:
Operational
Approximately 4 hours per day were dedicated to manual feasibility analysis, totaling 80 hours per month of repetitive and error-prone work.
Commercials
Planning failures could result in line stoppages, delivery delays and suboptimal sequencing, affecting productivity.
Financial
The lack of accurate analysis compromised the maximization of production capacity and generated additional costs in inventory management.
In a context of increasingly shorter delivery times, constant search for process optimization and constant challenges in the supply chain, the need for an automated and intelligent solution has become essential to ensure the company's efficiency and competitiveness. This was an ideal use case for the type of offering developed by BlueMetrics: a client with a clear need, with a strong impact on the company's performance, requiring an efficient, adherent and quickly implemented solution, in order to deliver concrete results in the short term.

Solution: linear programming for the automation and optimization of processes
The Tech Storm solution was designed to automate and optimize production planning in the factory. The technology uses an optimization algorithm based on linear programming to analyze production and inventory data in real time, ensuring greater accuracy and agility.
According to Diórgenes Eugênio, Head of Gen AI at BlueMetrics, “The Tech Storm project had several challenges, mainly because it was a very specific niche with detailed concepts. The initial meetings were crucial to the success of the project, as this was where the manufacturer’s team was able to show the entire process and what the factory’s pain points were within the sequencing process. After the first phase of understanding the problem and concepts, we worked to understand the data sources and how we could make the process automation viable. From that point on, we already knew how we would technically approach sequencing optimization, but we still needed to define some strategies to extract all the necessary information from a table with more than 400 rows and 400 columns. After a few attempts and meetings with the client’s team, we were able to optimize data extraction, ending up with five seconds for data collection and transformation. With the data structures ready, we applied the linear programming algorithm, which always sought to maximize the number of KNRs produced. After a few iterations, we arrived at a result that guaranteed the best assembly sequence for the production line. The participation of the client’s team was fundamental in building this solution.”
The basis of a good project is a reliable and resilient data structure. Therefore, a data and analysis pipeline was developed that uses the Prognose table, widely used in the factory, as its main source. This table allows operators to correlate part number balances with KNRs in production, enabling vehicle assembly according to parts availability.
The extraction and transformation of this data was performed in the first stage of the pipeline, converting it into optimized structures for the execution of the optimization algorithm. These new structures provide fundamental insights, such as KNRs pending analysis, updated part number balance and the list of components required to assemble each KNR.
With the information organized, an optimization algorithm based on linear programming was implemented. This algorithm was designed to maximize a specific objective: to produce the largest number of KNRs possible, efficiently using the available part number balances and viable combinations for assembly.
Finally, Tech Storm was developed taking into account three important pillars: the automation of data collection, making it faster and more reliable; the optimization of the decision-making process, in order to present the best production possibilities quickly and assertively; and a user-friendly, secure and intuitive interface, in order to facilitate the adoption of the solution among the different teams involved.
Main features:
Data Collection Automation:
Automatic extraction of information from the Prognose spreadsheet, including KNRs (vehicle reference numbers), component requirements and stock balances.
Efficient integration with existing customer systems.
Optimization Algorithm:
Calculation of the best production combination in just 6 seconds.
Maximizing the volume of vehicles produced considering stock restrictions.
Intuitive Interface:
Development of a dashboard in Streamlit, which presents results in a clear and accessible way.
Hosting in the AWS cloud environment, ensuring scalability and security.
How about developing a solution like this for your company?
Results:
The implementation of Tech Storm brought significant operational gains to the client, resulting in concrete and immediate financial results. Furthermore, Gabriel Casara points out that the proprietary blue4AI methodology provides, after the delivery of the solution, a vision of continuous optimization, in order to identify new opportunities for improvements and positive impact on the business.
Operational Efficiency:
Analysis time reduced from 4 hours to just 6 seconds (99.96% reduction).
Elimination of 80 monthly hours of manual work.
Increased accuracy of production planning.
Production Optimization:
Optimized production line sequencing.
Maximization of the number of vehicles produced per period.
Better use of available resources and reduced risk of unscheduled downtime.
Financial Impact:
Reduction of costs with inventory management.
Potential increase in revenue by optimizing production capacity.
Qualitative Benefits:
Greater predictability and agility in decision making.
Scalable and adaptable process for other production scenarios.
Technologies used
The Tech Storm solution was designed using AWS technologies, including:
AWS Services
EC2
Application Load Balancer
Languages, Libs and Frameworks
Python
Streamlit
Pulp
OpenPyxl
Pandas
Plotly
Conclusion
With Tech Storm, the manufacturer reinforced its commitment to innovation and efficiency, consolidating itself as a reference in the use of advanced technologies for the automotive sector. For BlueMetrics, this case was a great opportunity to demonstrate the way in which companies work, applying a proprietary methodology that provides great agility and adherence to projects, as well as agile and uncomplicated implementation, which emphasizes business vision and the generation of concrete, short-term results for the client.
Want to build a case like this for your company? Let's chat.
Discover some Use Cases .
About BlueMetrics
BlueMetrics was founded in 2016 and has already delivered more than 160 successful solutions in the areas of Data & Analytics, GenAI and Machine Learning for more than 70 companies in the United States, Brazil, Argentina, Colombia and Mexico. It has its own methodology and a multidisciplinary team focused on delivering solutions to real challenges in the business world.
Comments